製造業や工場を保有している企業・業界の中で話題になっているスマートファクトリー。本記事では、スマートファクトリーがどのようなものなのか、メリットや導入事例、推進する流れと併せて注意点も解説します。スマートファクトリーの導入を検討している企業の方は、ぜひご一読ください。
<この記事の要約>
スマートファクトリーとは「IoT・AI・ロボを使って工場を可視化・最適化する次世代の生産拠点」
製造ラインの稼働状況をリアルタイムで把握し、可視化・自動化・予知保全を実現。高度な生産性と品質を維持しつつ、新たな付加価値創出を可能にする取り組みになる。
直面する課題は「セキュリティ・現場理解・人材の整備」になる
データ連携とセキュリティ確保の必要性が高まる一方、現場におけるデータ利活用の習熟と、適切なスキルとマインドをもつ人材確保が導入のハードルになる。
推進のステップは「現状把握→構想策定→段階導入→共感形成→運用実装」の流れ
As‑Is/To‑Beから現場の課題を明確化し、試行と成果共有を重ねながら段階的に技術を導入し、最終的に運用設計までを現場主導で実装するプロセスになる。
スマートファクトリーとは
スマートファクトリーとは工場をデジタル技術によって改革していき、受発注や生産管理などのサプライチェーン、研究開発・商品企画のエンジニアリングチェーン、製品の製造からその後の流通、アフターサービスなどにおいて、業務効率化や品質・生産性の向上、新たな付加価値の創出を目指していく一連の活動や、そのような状態の工場のことをさします。
具体的には、機械をネットワークにつなぎ作業員のスマートフォンで稼働状況やエラーを検知できるようにしたり、生産設備から得られた大量のデータを解析し品質を左右する重要な管理ポイントを見極めることで、より効率的に現物確認の実効性を高めたり、データ活用により今までできなかった製品を生み出したりといったソリューションがあります。
インダストリー4.0との関係
スマートファクトリーは、2011年にドイツ政府が発表したインダストリー4.0という産業政策の中で重要なコンセプトとして出てきます。ドイツは昔からものづくりが盛んで多くの工場を保有し、多くの熟練技術者が働いています。
アメリカなどでは生産機能を新興国に移管しコスト削減を実現していますが、ドイツは生産現場を他に移すと製品開発能力もやがて失われ競争力も落ちると考え、国内に生産機能を残すためにインダストリー4.0を推進しようとしています。
その中で「製品開発に関する工程の標準化」、「製品に関わるシステムやデバイスのネットワークによる統合」、「新規ビジネスモデルや製品の創出」などを掲げています。
スマートファクトリーとは単なる製造現場の自動化にとどまらず、
- 研究開発や製品設計に資する情報の取得といったエンジニアリングチェーンの革新
- 原材料の調達、製品の納入、市場投入後のアフターフォローなどに資するトレーサビリティの確保
などをめたサプライチェーン全体における革新を指す、非常に重要な概念となっています。
インダストリー4.0が提唱されてから10年以上経ち、現在ではドイツがインダストリー4.0に続く方針として「2030 Vision for Industrie 4.0」を発表したり、欧州委員会が「インダストリー5.0」を提唱したりするなど、インダストリー4.0に次ぐ概念を各国が提唱し始めています。「インダストリー5.0」は「人間中心」「サステナブル(持続可能)」「レジリエント(回復力)」をキーコンセプトに人間のニーズを起点として気候ニュートラルに向けた循環型アプローチへの変革や、人々の生活を破壊的変化から守ることなどが提唱されている。
スマートファクトリーのレベル
経済産業省が公開している「スマートファクトリーにおけるサイバーセキュリティ確保に向けた調査(2021年12月)」によると、スマートファクトリーにはデータの活用度合いに応じてレベルがあるとされています。
※資料:「スマートファクトリーにおけるサイバーセキュリティ確保に向けた調査」経済産業省2021年12月を基にエクサウィザーズで作成
レベルとは、以下の5つです。
- レベル0:従来の工場
- 情報がまだ活用されていない状態
- レベル1:データの収集・蓄積
- 有益な情報を見極めて収集して状態を見える化し、得られた気付き知見・ノウハウとして蓄積できる状態
- レベル2:データによる分析・予測
- 膨大な情報を分析・学習し、目的に寄与する因子の抽出や、事象のモデル化・ 将来予測ができる状態
- レベル3:データによる制御・最適化
- 蓄積した知見・ノウハウや、構築したモデルによる将来予測を基に最適な判断・実行ができる状態
- レベル4:動的な自律制御
- 複数の工場または事業者が接続し、解析結果や予測を基に、各主体が自律的かつ動的に制御できる状態
例えば、製品の品質安定化を目的とする場合で考えてみましょう。
レベル1では、設備にセンサーを取り付けることで、どのような品質の製品を作った時に、設備はどのような状況だったのか、どのような設定値だったのかというデータの取得ができます。
レベル2では、収集したデータを解析し、品質のばらつきの要因を特定したり、質を上げたりするための設定値や条件を特定することができます。
レベル3では、レベル2で特定し構築した改善モデルを実際に適用し、製品の質を最大化させる条件・設定値を最適化することで低品質な製品を減らしたり質のばらつきを抑えたりすることを目指します。
レベル4では、レベル1~3のデータや改善モデルを複数の工場などで共有し、最適なモデルをシステムが自律的に制御して適用していくことで最小限の工数で多くの工場において品質のばらつきを抑えることを目指します。
以上のようにスマートファクトリーにもレベルがあるため、自社のスマートファクトリー化のロードマップを考える上で参考にしましょう。また、最終的にレベル4に行くことを想定した上で要件を定義することも重要です。
参考:『スマートファクトリーにおけるサイバーセキュリティ確保に向けた調査』経済産業省 2021年12月
国内のスマートファクトリーをとりまく現状
経済産業省が2022年5月に発表した「2022年版 ものづくり白書」では、ものづくりの工程・活動においてデジタル技術を活用しているかどうかについて以下のような結果になっていました。
- 既に活用している:67%
- (活用していない、又は該当する工程・活動がない:31%
しかし、その大部分が大企業であり、中小企業の実施状況は伸び悩んでいるのが現状です。また、スマートファクトリー化を進めるにあたって、実施済み・未実施の企業ともにデジタル技術の導入に必要なノウハウや人材、コストの不足を感じているようです。このことから、日本の製造業ではスマートファクトリー化の必要性が認識されつつある一方、実施に難航している企業が多いと言えるでしょう。
日本では企業の規模を問わず、少子高齢化による人材不足が深刻化しています。また、熟練の技術者が高齢化していることに加え、若手の人材育成が遅れているため、技術継承が困難になりつつあります。
急激なネットワークの発達により市場はグローバル化し、価格競争だけでなく生産速度もこれまで以上の速度が求められるようになったことで、既存の製造では企業が国際競争に打ち勝つことは困難です。
多様化しつつある現代社会は環境や消費者のニーズも変動しやすく、臨機応変に対応できるかが企業生命に影響します。
これらのことを踏まえ、スマートファクトリー化は、工場を持つ企業にとっては取り組むべき重要事項と言えるでしょう。
参考:『 2020年版 ものづくり白書』経済産業省 2020年5月
参考:『 2022年版 ものづくり白書』経済産業省 2022年5月
工場をスマートファクトリー化する目的・メリットと具体例
工場のスマートファクトリー化には、様々なメリットがありますが大きく7つに分類して紹介します。具体的なメリットを知ることで、自社のスマートファクトリー化を推し進めるイメージも沸くため、確認しておきましょう。
①製品の品質向上・安定化
工場をスマートファクトリー化するメリットは、設備や社員の作業状況、製品の設定値といったあらゆるデータを見える化し、課題を改善することで製品の品質向上安定化できることです。具体的には歩留まりの改善、品質のばらつきの改善、設計仕様や生産方法の修正による製品特性の向上を目指します。
例えば、センシングによって人の作業情報といったデータがデジタル化され解析用データとして利用できるようになることでそこに含まれるノウハウや個人差によるばらつきなどの課題をあぶりだし、対策を打てるようになります。それにより。
また、スマートファクトリー化することで、データベースとして利用できるデータの種類が増えるため今まで以上に解析・改善ができ、品質のばらつきの減少、製品品質の安定に繋がるでしょう。
センサー機能や通信機能から実稼働状況を確認し、元の設計データを照らし合わせれば、設計内容や製造方法の修正・改善にも対応できます。
②コストの削減
工場のスマートファクトリー化は、製造過程でかかるさまざまなコストの削減にも効果があります。
材料の使用量を削減したり、在庫を最小化したり、設備の監視・点検を効率化したり、生産計画最適化により投入リソースを最小化したりする例があげられます
代表的な例として、MES(製造実行システム)などの生産管理システムを導入し、生産計画・実績データを蓄積、受注・生産・出荷の計画・実績データなどのデータを分析し需給予測を行い、予測した需要・供給データに基づいて在庫や投入リソースを最適化することで、人件費や生産に必要なエネルギーなどのリソースも最小限に抑えられますし、在庫が余ってしまうこともありません。
在庫の設定なども含めた各現場レベルでの担当者のノウハウにゆだねた最適化対応も全体最適化となるようにシステム化することで、経営目線での判断が現場に滞りなく反映しやすくなることもスマートファクトリー化の利点です。
③生産性の向上
設備や人材の稼働率を向上させたり、人の作業を効率化・自動化させたり、負担を軽減させたり、設備故障に伴う設備の停止を削減したりすることで生産性の向上にもつながります。
例えば、設備や人の稼働状況・作業の進捗状況をデータ化し、非稼働時間を短縮すれば、生産ライン全体の稼働率も上げることができるでしょう。また、を取り入れることにより、情報の入力・表示・修正といった現場業務の負担を低減しつつ有効なデータを取得することができます。設備が故障してしまうなどの万が一の事態に備えてモニタリングを実施しておけば、トラブルの予兆を検知して稼働停止を防止できます。
④早期の製品開発・量産体制の推進
スマートファクトリー化のメリットです。製品の開発・設計を自動化したり、生産ラインの設計・構築化の短縮化をしたりすることで実現します。
例えば、AIに過去の設計事例を学習させるケースでは、構造仕様をモデル化し、過去の製造におけるトライ&エラーの結果や、不良発生における構造仕様の特徴やその対策結果などを学習し、新規仕様における課題になりそうなポイントの指摘や修正など製品の開発・設計を自動化できます。また、開発・設計・生産の情報をデータベース化しておけば、仕様変更時にも迅速に対応できるでしょう。生産ラインシミュレータなどを活用することで、生産ラインの設計・構築の短縮化も実現できます。
⑤人手不足への対応(技能継承や多様な人材活用)
多様な人材を活用したり、様々なデバイスを駆使したり、技能伝承に取り組むことで人手不足に対応できます。
例えば、HMD(ヘッドマウントディスプレー)やスマートウォッチ、生体センサーなどのアシストデバイスを導入することで、人材の能力を拡張・補完することが可能になり、特性の異なる多様な人材を活用することができます。
また、熟練度が高い社員のノウハウや知見を、データ化し具体的に優れている点などを明確化します。技能の可視化が進めば簡単に熟練技能を他の人に引き継ぐことができるようになります。熟練技能を人と同じように周囲の状況に応じて最適な動作を自律的に実行するスマートロボットに学習させることができれば後継者がいなくても技術が消失することはありません。
⑥新たな付加価値の提供
製品に新たな付加価値をつけることもスマートファクトリーのメリットです。
データ化した情報を工場間、部門間で共有することで、さまざまな顧客のニーズに対応した新たな製品・サービスを生産できます。また、内部だけでなく他業種の企業と連携をとることで、自社の加工技術を高められるでしょう。
製品にセンサーや通信機能を搭載すれば、使用状況や評価に応じてユーザーのニーズに沿った性能・機能の向上や新機能追加も可能になりますし、アフターサービスの新規提供や別サービスの開発にもつながります。
⑦リスク管理の強化
スマートファクトリーはリスク管理の強化にも効果的です。
例えば、製品にRFIDを搭載して、加工・組立・検査・出荷のデータを取得・蓄積することで、製品個体毎の品質を証明(トレーサビリティ)できるようになります。
また、不具合などが発生した際に製造プロセスから課題を抽出して原因を特定し、影響を最小限にとどめ早期改善に動けます。
スマートファクトリーの乗り越えるべき課題
スマートファクトリーには多くのメリットがある一方で、導入に至るまで、導入した後の運用においていくつか課題もあります。
人材の課題
スマートファクトリー化において、大きな課題の一つが人材の課題です。スマートファクトリーでは多くの機器やシステムを用いて多くの種類・量のデータを活用することが求められます。機器やシステムを改修するのか、システムごと入れ替えるのか、複数のシステムやデータをどのように統合・連携させるのかといった検討事項が多く発生します。
それにはハードウェアエンジニアリングやソフトウェアエンジニアリング、データベースや分析・統計のスキル、AIなどの専門スキルに加え、関係者を説得・調整しながら巻き込んで進めていくリーダーシップや問題解決能力においても高い水準が求められるため、そうした人材の獲得や育成はスマートファクトリー導入に対する大きな課題となっています。
しかし、製造業においては年々人材不足が深刻化しており、『2021年版 ものづくり白書』によると 国内の製造業就業者数については、2002年の1,202万人から2020年には1,045万人と、約20年間で157万人減少しており、優秀な人材を採用するのはより難しくなってきています。
解決策としては、高い水準の技術力を保有した人材の採用・育成や外部の支援会社による支援があげられます。人材の採用・育成はハードルが高く時間もかかるため、早期にスマートファクトリー化を推進したい場合は外部の支援会社への依頼を検討してみましょう。また、長期的にスマートファクトリーを運用していくためには採用や社内の人材の育成も必須のため平行してしっかりと取り組んでいきましょう。
DX人材の育成方法については、「DX人材育成の方法を大公開。DX人材育成5つのステップはスキルと素養の可視化から」をぜひ参考にしてください。
セキュリティの課題
工場のシステムは内部に限ったネットワークとして構築され、外部ネットワークと接続されないことが前提となって設計されているところも多いでしょう。しかしスマートファクトリーでは多くのシステム・デバイスをネットワークに繋げることになるため、新たなセキュリティリスクが発生します。そのためスマートファクトリー化と並行してセキュリティ対策を実施していく必要があります。
DXとセキュリティの関係については、「DXで重要なセキュリティ対策とは?最新のセキュリティトレンドも紹介」をぜひ参考にしてください。
スマートファクトリーで利活用されるデータごとのリスクとして以下のようなものがあります。
利活用データ分類 | データの窃取・改ざん等のリスク |
センサーデータ | 部分的な窃取ではフィールド内からの具体的な機密漏洩に至る可能性は低い。改ざんされた場合、情報が撹乱されるリスクはあるが、正常稼働に直接影響するおそれは少ない。 |
静止画データ | 窃取された場合、フィールド内の機器や組立等の機密が(静止画情報という形で)漏洩する。 |
動画データ | 窃取された場合、フィールド内の機器や組立等の機密が(動画情報という形で)漏洩する。 |
制御コマンド | 改ざんされた場合、誤った制御情報により正常稼働できなくあるおそれがある。 |
エンジニアリング設定 | 投入するプログラムへのマルウェア混入等により正常稼働できなくあるおそれがある。 |
機器状態値 | 部分的な窃取ではフィールド内からの具体的な機密漏洩に至る可能性は低いため、リスクは比較的低い。 |
生産計画値 | 窃取された場合、生産計画という内部情報が漏洩するおそれがある。改ざんされた場合、情報の解釈を誤るおそれがある。 |
集計分析データ | 窃取された場合、(情報処理後の)非公開情報が漏洩するおそれがある。改ざんされた場合、情報の解釈を誤るおそれがある。 |
出典:『スマートファクトリーにおけるサイバーセキュリティ確保に向けた調査報告書』株式会社三菱総合研究所 2021年3月26日
必要なセキュリティ対策としては、外部からの不正アクセスの防止、アクセスする社員やデバイスの認証、各機器のマルウェア対策、脆弱性の管理、工場ネットワークとその他オフィスネットワークの分離などがあげられます。
スマートファクトリーの事例
スマートファクトリーの事例を、5つ紹介していきます。
なお、製造業全体の事例については、「製造業におけるDXの課題とポイントを最新事例と共に紹介!」で紹介していますので、合わせてご確認ください。
BMW
実施内容・成果
BMWはNVIDEAと共同で未来の工場を創造しています。BMWは様々なカスタマイズが可能で1台当たり2,100通りの組み合わせが存在します。そのため工場の再設計や再構築が頻繁に必要になります。これをNVIDEAが開発・提供している「Omniverse」というプラットフォームを活用し、デジタルツインと呼ばれる現実の工場や設備、生産ラインを忠実にコンピュータ上で再現する技術を用いることで解決しています。具体的には
- デジタルヒューマンを使った事前のシミュレーションによる安全性の向上
- 竣工前の工場をデジタルで作って設備や作業をシミュレーション
- 操業時のロボットの遠隔監視と適切な対応
などを行っています。
また、AIを活用したシミュレーションや自律型ロボット、予測保守、ビッグデータ分析など様々なソリューションも導入しており、自動車製造における多くの工程で柔軟性と正確性を高め最終的には計画プロセスを30%効率化できるとしています。
参考にしたいポイント・アクション
- ロボットと人との共同作業を実現している点は参考にしたいポイントです。BMWの工場では作業員5万7000人がロボットと職場を共有しながら作業しています。ロボットからのアラート通知を受け取ると、作業員がロボットを遠隔操作し、カメラで確認しながらロボットを誘導して修正するといった連携が行われています。
参考:『NVIDIAとBMW、現実世界と仮想世界が融合された未来の自動車工場「デジタル ツイン」を実演』2021年4月21日
Factory-IoT(デンソー)
実施内容・成果
デンソーでは、2020年「ダントツ工場」実現に向けて業界で初めて、世界各国にある130もの工場をIT、IoTでつなぐ「Factory-IoTプラットフォーム」を自社開発しました。各地にある工場の機器からデータの収集や蓄積をすることで、生産の改善や稼働状況の改善などさまざまなことに用いることができます。
データの活用によって設備や人の稼働率が向上し、改善にかかる時間が短縮できるようになりました。
各種デバイスを連携させれば、設備や生産ラインに異常があった際に、リアルタイムで管理者や作業者に情報を共有でき、万が一の際も迅速に対応することが可能です。
参考にしたいポイント・アクション
・ドイツ政策のインダストリー4.0が重視している「つなぐ」と、アメリカのIICが重視している「分析する」のどちらか一方だけでなく、両方の良い点を抑えたうえでものづくりを知る人に有益な情報を提供することも重視し、仲間づくりや標準化を推進しています。
参考:経済産業省:「スマートファクトリーロードマップ」〜第4次産業⾰命に対応したものづくりの実現に向けて〜 2017年5月31日
参考:株式会社デンソー:デンソー、世界130の工場をIoTでつなぐFactory-IoTプラットフォームを開発 2020年10月5日
組織づくりのコツについては、「【決定版】人材育成ロードマップの作り方|効果的な組織と個人のキャリア成長法」をぜひ参考にしてください
株式会社東芝
実施内容・成果
東芝では「生産技術センター」という東芝の製品を効率よく低コストで高品質に生産する研究開発機関が中心となりスマートファクトリー化を推進しました。
システム導入だけでなく、IE(Industrial Engineering)と呼ばれる論理的な分析によって、生産性を向上する手法を推進できる人材を育成することで、各拠点の中心となって品質管理や作業管理をはじめ、目標設計や基準達成ができるようになりました。
東芝では各工場のスマート化だけでなく、バリューチェーン全体がつながることで、KPIの明確化、デジタル化レベルの向上、スマートマニュファクチャリングの3つのステップを全て実現し、取り組んでいます。
参考にしたいポイント・アクション
・スマートファクトリー化の取り組みは、工場の中だけでは達成できないとし、設計や生産、営業担当者、総務担当者なども含めて議論をして「ありたい姿」のビジョンを描き、関係者全員が腹落ちできるところまで議論をして、合意形成を行いながら進めるようにしました。そうすることで個別最適になることを避け全体最適になるスマートファクトリーを目指しています。
参考:経済産業省:「スマートファクトリーロードマップ」〜第4次産業⾰命に対応したものづくりの実現に向けて〜 2017年5月31日
参考:株式会社東芝:製造業DXに向けた東芝の「スマートマニュファクチャリング」の取り組み(後編) 2022年1月28日
ハーレーダビッドソン
実施内容・成果
アメリカの大手オートバイメーカーのハーレーダビッドソンは、カスタマイズ(改造)して自分だけのハーレーを作れることが大きな特徴でファンから指示されています。従来は、標準となる製品は内製で生産し、カスタマイズは「カスタム専門店」などの外部に任せるという方針を取っていました。
しかし2011年に、スマートファクトリー化と共に、初めからカスタマイズした状態の製品も注文できるような仕組みが誕生しています。
これは、様々なものをデジタル化・IoT化して効率化・自動化を進めていく中でカスタマイズオーダーもサプライチェーンの中に組み込むことができるようになったことが大きな要因です。
これにより、消費者は約1300種類の選択肢の中から好きにカスタマイズして注文できるようになっただけでなく、工場の部品在庫は従来の8~10日間の保持から3時間になり、コストが7%減、人員数も800人ほど減、生産リードタイムは21日間から6時間と大幅な効率化を達成しました。
参考にしたいポイント・アクション
・スマートファクトリー化と共に、ユーザーのニーズに沿ったサービス提供ができるようにビジネスモデル自体を改革した点は、単なる効率化・自動化に留まらないスマートファクトリーの例として参考になります。
参考:『海外事例にヒントあり! 日本の製造業が「ものづくりIT」で目指すべき姿』TECH+ 2020年4月24日
参考:『マス・カスタマイゼーション(一品大量生産)をⅠoTで実現したハーレー・ダビッドソン』オートメーション新聞WEB 2016年4月6日
スマートファクトリー化を実現するステップ
スマートファクトリー化を実現するにはどうすればよいのでしょうか。実現に必要な6つのステップに分けて解説します。
①スマート化の目的・ゴールを明確にする
まずは、を考えましょう。導入したい技術を先行して考えても、目的にそぐわない可能性があります。そのため、まずは目的とゴールを考え、どのような技術が必要なのかを比較・検討することが大切です。
スマートファクトリー化の目的は主に
- 品質の向上
- コスト削減
- 生産性の向上
- 製品化・量産化の期間短縮
- 人材不足・育成への対応
- 新たな価値提供・新規サービス創出
などがあります。
目的も工場で生産している製品や、そもそもの工場の目的によっても変わってきます。
例えば大量の製品を効率的に高品質に作ることが求められている部品工場などでは、効率やコスト削減生産性の向上がゴールになるでしょう。
また、工場内で製品生産のプロセスを上流から下流まですべて担っている場合は、新規価値の提供やビジネスモデルの変革が目的になる場合もあるでしょう。
このように工場自体の目的やさらにその上の経営・事業方針とも連動してくる部分になるため、経営やその他関係者も合意を取りながらゴールを設計するようにしましょう。
②スマート化の内容・範囲・規模を明確にする
目的などが明確にできたら、次はスマート化の内容や対象について具体的に考えます。
まず大枠として、目的や現状から難易度と導入インパクトでスマートファクトリーの内容を分けます。その上で難易度が低く、インパクトが大きい(ROIが高い)内容について具体的な取り組みを検討していきましょう。
施策ごとの内容明確化イメージ ※エクサウィザーズ作成
製造工程、業務範囲、技術、などの細かい部分まで明確かつ具体的に定義し、そこにかかるコストやROIを概算的に想定することですることができるでしょう。社内だけで考えることが難しい場合は、外部の専門家に依頼して助言を求めることも考えましょう。
③関係部署と連携し合意を取る
スマートファクトリー化は関係する部署が多いため様々な部署と密に連携をとりながら進めていく必要があります。
ビジネスモデルの変革に繋がるスマートファクトリー化であれば経営層や開発・設計部門・営業部門などと連携しておく必要があります。
生産期間の大幅な短縮を行う場合やセキュリティ周りで大きい変更がある場合顧客にも早い段階で周知・調整する必要があるでしょう。
効率化によるコスト削減を狙う場合で人件費の削減も視野に入れている場合や、人材の採用や育成も行う場合は人事と連携をする必要が出てきます。
このように多くの関係者を巻き込みながら進める必要があるため、経営が強いビジョンを持ち、全社に発信しながら企業全体の目標として取り組むようにしなくてはなりません。企業全体で取り組むことでスムーズに推進できるようになるでしょう。
④システムを選定しスモールスタートで始める
パートごとに具体的な目標を立てた後は、どのような機能・システムが必要になるかを絞り込んでいきます。あくまで目的から逆算し必要な機能を考えつつ、後々機能を拡張したい時にも対応できるように意識しながら要件を定義していきます。そして最初はスモールスタートで実施する計画を組みましょう。
スマートファクトリー化にはエラーやトラブルはつきものです。理論的には「このシステムからはこの頻度でこういうデータが取れる」と考えていても通信環境やセキュリティの問題、データにノイズが入るなどの理由で正確に取れない場合も出てきます。
よってあらかじめ堅牢なシステムを作るのではなく、エラーは出る前提でスモールに実施していき、諸々検証ができてきたら強化・拡張していくというやり方が良いでしょう。
また大規模な既存設備の改修をしなくてもIoTツールを後付けすることで対応できる可能性もあります。様々な手法を選択肢に入れて検討を進めましょう。
⑤トライアルを繰り返し、他工程にも展開し、効果を最大化
リスクが小さく、導入効果が見込めるところから取り組むことで効果を実感しやすくなり、取り組みがいが得られ、周りの関係者の協力も得やすくなります。参考にすべき価値あるデータを⾒極め、システム・運⽤の完成を少しずつ目指していきます。
各工程でスモールスタートしていきつつ、徐々に他の工程にも展開していきます。その中で、各工程間で相互に調整をかけて精度を高めつつ、徐々に対象を拡大してきます。それを広げていけば最終的には全行程のデジタル化ができ、より正確な予測や効率化、品質向上が実現できます。
例えば、多岐にわたる工程の中のうち、「プレス工程」で金属板の傷を画像解析で検知するソリューションを導入し、PDCAを回し精度を上げます。次に「溶接工程」「塗装工程」とソリューションを広げていきます。
その中で、「塗装工程」のソリューションの精度を上げるために前工程である「溶接工程」のデータから調整をしてより統合的に精度を上げるといったことも考えられます。
そして最終的には全行程をデジタル化して統合することで正確な予測や効率化・品質向上を実現することができるようになります。
このようにスモールスタートしてPDCAを回しながら徐々に対象を広げて全体に広げていくことで少ないリスクでスマートファクトリー化を推進できます。
⑥導入効果を社員に共有
導入効果を継続的にモニタリングし、社員にできるだけ早い段階から共有していきます。小さな変化であっても、具体的な数値として変化が分かることで、社員のモチベーションの向上や運用の定着につながります。
以上の手順でスマートファクトリー化を推進していくようにしましょう。
身近なルーチン業務からはじめられるDXとは?
自社のDXを推進しようと検討するものの、何から始めたらいいかわからない、また、社内の複数部署で合意形成を取る難易度が高い…と考えている方へ。
まずは、「身近な業務のDX化」から検討するのが得策です。ぜひ、無料のお役立ち資料からご確認ください。
\こんな方におすすめの資料です/
- DXと言っても何をすればいいかわからない
- まずは身近なところからクイックにできるDXを試したい
- 目の前のルーチン業務を効率化したい
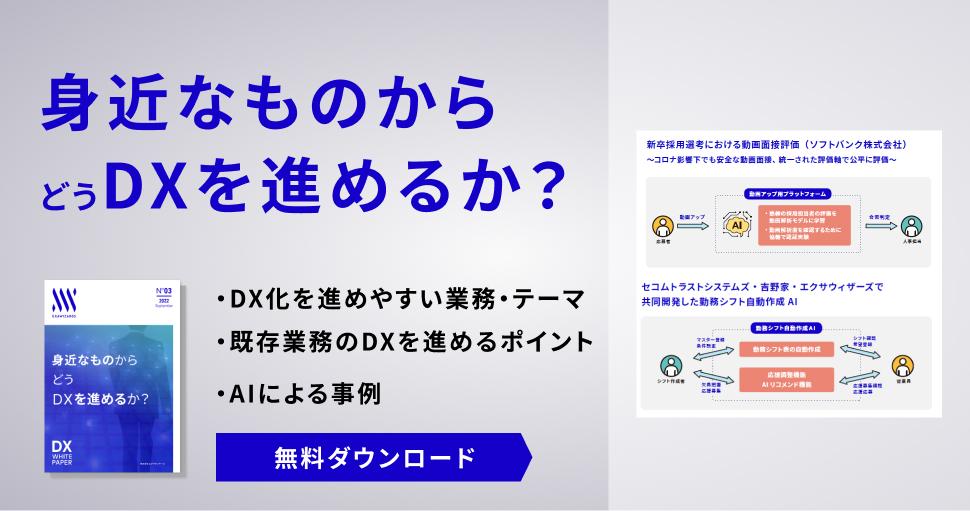
スマートファクトリーロードマップ
経済産業省は第4次産業⾰命に対応したものづくりの実現に向けて「 スマートファクトリーロードマップ 」を公開しています。
このスマートファクトリーロードマップでは、目的別にスマート化のレベルを3レベルずつ定義しており、どの順番で何をすればいいのかを整理してくれているので、ぜひ参考にしてみてください。
以下のように参考にしやすい工夫がされています。
- 品質の向上、コストの削減、⽣産性の向上など、⽇頃、企業が取り組んでいる⾝近な⽬的別に整理
- IoTなどのソリューションをどのように活⽤し、どのような状態を実現すればよいかがイメージできるよう3レベルでスマート化を整理
- 21個の先行事例が目的別に紹介されており、自社に目的に沿った先行事例を見つけやすい
また、スマートファクトリーの目的別にスマート化の手段や対象企業、スマート化対象のものづくりプロセス、スマート化のレベルが一覧で見やすくまとめられているものは以下からご覧いただけます。
スマートファクトリー化で重要なポイント
スマートファクトリー化には特に意識したい、重要な3つのポイントがあります。
①経営層の強いコミットメント
スマートファクトリー化は多くの時間と費用をかけ、全社員、時には社外も巻き込んでいく取り組みです。そのため、全員の共通認識が違っていたり、実施する意図が浸透していなかったりすると、「反対意見に押されスマートファクトリー化に踏み切れない」「途中で手段が目的化し当初の目的を達成できない」、「部署間で軋轢が生じ頓挫する」、「考慮漏れが発生し中途半端な状態になる」、「開始まで漕ぎつけてもその後の実運用が回らない」といったことに繋がります。
そうならないためにも、経営層が強い意志を持ってコミットする、ビジョンを発信する、時には社内調整などにも入り実現をサポートするといったことが重要になります。
経営層がコミットすることで意思決定のスピードや規模が上がり、関係者を巻き込みやすくすることでスムーズにスマートファクトリー化が実現しそのパフォーマンスも工場するでしょう。
②ものづくりとデジタル両方を活用できる人材の育成
スマートファクトリー化は、デバイスや設備・ものづくりに関するスキルと・経験と、デジタルや分析に関するスキル・経験の両方が重要になります。そのため、ものづくりとデジタルの両方に理解がある人材を採用・育成することが大切です。
しかし、製造業や工場での就業を志望する人材は減少傾向にあるため「デジタルに詳しい人を採用して、ものづくりに関するスキルを覚えてもらう」ことのハードルは高い可能性があります。また、デバイスや設備・ものづくりに関するスキル・経験は現場で実際に設備に触れて身に着くことも多いため学習ハードルも高いでしょう。
一方、デジタルや分析に関するスキルは比較的身に付けやすいと言えるため、デバイスや設備・ものづくりに関するスキル・経験がある既存社員にデジタルや分析に関するスキルを身に着けるように育成するのが良いでしょう。
もちろん、デジタル・分析のスキルを持った人の外部採用を強化することで良い人材が採用できるかもしれないので平行して行うこと自体は問題ありません。
③自社にあったスマートファクトリーを
スマートファクトリーには目的ごとに様々な手法や扱うデータがあり、扱っている商品や解決すべき課題によって適切な技術は異なります。そのため、たとえ同業であっても他社の真似をすれば解決できるわけではありません。自社にあった最適なスマートファクトリー化を進めるためにも、具体的な改善案を出し、必要な機能などを選びましょう。
例えば、
- 既存の設備やシステム、扱っているデータに最適なシステムや機能は何か
- 現在の社員のスキルや特性的に向いているシステムや機能・オペレーションは何か
- 社内のセキュリティ標準をクリアするソリューションか
- 生産品の特性に合ったデバイスか
など、自社に合っているかどうかは多様な観点で検討しましょう。
スマートファクトリーの技術基盤
スマートファクトリーを実現する基盤となるのが、IoT・センサー技術、AI・機械学習、エッジコンピューティングといった先端テクノロジーです。
これらの技術は単体でも価値がありますが、統合して活用することで相乗効果を生み出し、製造業のDXを加速させます。適切な技術選択と組み合わせにより、生産性向上、品質安定化、コスト削減などの効果を最大化できます。
IoT・センサー技術
スマートファクトリーの基盤はIoTとセンサーであり、これにより設備状態や環境のリアルタイム監視が可能になります。適切なセンサー選定と配置が製造プロセスの可視化と最適化の鍵です。様々な産業用センサーは工場の「目」と「耳」の役割を果たします。
センサー種類 | 用途 |
---|---|
温度センサー | 機械設備の過熱検知、製品品質管理 |
振動センサー | 機械の異常検知、予防保全 |
画像センサー | 外観検査、動作監視 |
電力センサー | エネルギー消費監視、効率最適化 |
IoTデバイスのネットワーク構築では通信プロトコルの選択が重要で、工場の規模や環境に応じてWi-Fi、Bluetooth、有線LANなどを適切に組み合わせる必要があります。セキュリティ対策も忘れてはならない重要要素です。
AI・機械学習
製造現場におけるAI・機械学習は膨大なデータから価値ある知見を引き出し、意思決定を支援します。
AI活用領域 | 実現方法 | 期待効果 |
---|---|---|
品質予測 | 製造パラメータと品質の相関分析 | 不良率低減、歩留まり向上 |
異常検知 | 正常パターンとの乖離検出 | 設備故障の早期発見 |
需要予測 | 過去の生産・販売データ分析 | 在庫最適化、生産計画効率化 |
画像検査 | ディープラーニングによる特徴抽出 | 検査精度向上、人的ミス削減 |
AI導入には質の高い学習データが不可欠であり、センサーの異常値除去やノイズ処理などのデータクレンジングが精度向上の鍵となります。現場の知識を持つエンジニアとの連携も成功の重要要素です。
エッジコンピューティング
製造現場では即時性が求められるため、データ発生源近くで処理を行うエッジコンピューティングが重要性を増しています。リアルタイム性と信頼性の両立が必要な製造現場では不可欠です。
処理タイプ | 適用場面 | メリット |
---|---|---|
エッジ処理 | 即時対応が必要な異常検知 | 低遅延、通信断時も継続稼働 |
クラウド処理 | 長期的なデータ分析、AIモデル更新 | 豊富な計算リソース、全社データ統合 |
ハイブリッド処理 | 一次判断はエッジ、詳細分析はクラウド | バランスの取れた処理効率 |
エッジAI | 画像認識、音声解析 | ネットワーク負荷軽減、プライバシー強化 |
製造現場でのエッジシステム構築には、必要な処理能力と電力効率のバランスを考慮した機器選定が重要です。また、エッジデバイスのセキュリティ対策も忘れてはならない要素となります。
また、工場内ではセキュリティ上の理由や物理的制約によりインターネットへの常時接続が困難な場合があるため、オフライン環境でも安定稼働できるエッジデバイスの選定が不可欠となります。
投資対効果と予算計画の考え方
スマートファクトリー化を進める際には、投資対効果(ROI)の見極めと適切な予算計画が成功の鍵です。多くの企業がデジタル投資に踏み切れない理由は、効果の不確実性や投資回収期間の見通しが立たないことにあります。
効果的な投資計画を立てるには、初期投資だけでなく、運用コスト、人材育成費、システム更新費など、ライフサイクル全体を見据えた予算設計が不可欠です。
<投資対効果の具体例>
投資項目 | 予算割合 | 回収期間目安 | 主な検討ポイント |
---|---|---|---|
ハードウェア | 30-40% | 1-3年 | 既存設備の改修か新規導入か |
ソフトウェア | 20-30% | 2-4年 | パッケージかカスタム開発か |
ネットワーク | 10-15% | 3-5年 | 有線/無線、セキュリティ対策 |
人材育成 | 15-20% | 長期的効果 | 内製化と外部委託のバランス |
予備費 | 5-10% | – | 想定外のリスク対応 |
投資効果を最大化するには「小さく始めて大きく育てる」アプローチが効果的です。投資回収が早く、成果が見えやすい領域から着手し、リスクを分散させながら確実に成果を積み上げていきましょう。
定量的効果と定性的効果の両面から評価することで、経営層を含めた社内の合意形成も容易になります。
投資計画立案時のポイント
- 現状課題の明確化と優先順位付け
- 段階的導入計画の策定
- 複数のシナリオ検討
- 隠れたコストの把握
- 定量的KPIの設定
- 定期的な効果測定と計画見直し
- 成功事例の横展開計画
最後に忘れてはならないのは、スマートファクトリー化は単なる設備投資ではなく、企業文化やビジネスモデルの変革を伴うものだということです。投資効果を最大化するには、技術導入だけでなく、人材育成や組織変革も含めた総合的なアプローチが必要となります。
DX人材育成における、ROIの考え方・ポイントを大解剖
DX投資、人材育成は目的や投資対効果の考え方が異なります。
では、DX人材の育成に取り組む上でROIとどのように向き合うのが適切なのでしょうか。
本資料は、DX推進担当者向けに、DX人材育成を推進する上で重要な考え方3つをお伝えします。
DX人材育成の育成計画や目標を策定する際の参考としてお役立ていただけますと幸いです。\こんな方におすすめの資料です/
- 人材育成におけるROIとの向き合い方がわからない
- 役員陣に対して、費用対効果の説明がうまくできない
展示会でスマートファクトリーを体験
スマートファクトリーを推進する上で、様々な設備・機械、ロボット、センサーなどを実際に見てみたいという方は展示会に足を運ぶことをおすすめします。様々なソリューションを提供している企業の商品を実際に見ることができます。
スマートファクトリーJAPAN
2024年2月に開催する日刊工業新聞社主催の「スマートファクトリーJAPAN」は、スマートファクトリーを実現するうえで欠かせない情報管理・処理システム、製造設備・装置、その他生産工場に関する技術・製品の展示会です。
2022年はオフライン・オンラインのハイブリッドで開催され、2022年は同時開催された展示会と併せてリアル展示の来場者は36,852人、オンライン展示は42,410人も来場しています。
参考:『スマートファクトリーJAPAN2024』日刊工業新聞社
スマート工場EXPO
2024年1月で第8回を迎えるRX JAPAN主催の「スマート工場EXPO」は、スマート工場・スマート物流を実現するためのIoTソリューション、AI、FA/ロボットなどの最新技術・ソリューションが一堂に出展する専門展です。来場する製造業の製造・生産技術、工場・物流関係者と出展企業との商談・技術相談の場です。
2023年は同時開催された展示会併せて74,193人も来場しています。
※2023年2月時点の情報です。
まとめ
スマートファクトリー化にはさまざまなメリットがあり、目的ごとにとるべきアプローチも非常に多様です。
しかし、自社に合った機能が導入できなければ、満足な効果を得ることはできずかえって大きな機会損失を生む可能性もあります。
適切な順序で、実際に新しい技術に触れながら、人材育成やセキュリティ、社内の情報共有といった間接的に考慮すべき点もしっかりと意識しながらスマートファクトリー化を推進していきましょう。
